To meet their mandates, water utilities must not only know where their assets are and how they relate to each other, but also how they relate to the infrastructure and operations of other departments and agencies, such as transportation and transit.
Nowhere is this more important than in a large public construction initiative like the building of the Eglinton light rail transit (LRT) in Toronto. This is where the biggest water system in the country meets the largest transit infrastructure build in the country. That’s a lot of moving parts.
Toronto Water, a division of the City of Toronto, is one of the largest water, wastewater, and stormwater utilities in North America, with approximately 6,000-kilometres (km) of watermains) servicing more than three million residents and businesses. It maintains and services assets worth approximately $28 billion, including: four water and four wastewater treatment plants, 4,100-km of sanitary sewers, 5,000-km of storm sewers, and 1,400-km of combined sewers.
Metrolinx is a Crown agency that manages and integrates road and public transport in the cities of Toronto and Hamilton and their suburbs and is currently building the Eglinton Crosstown, an LRT corridor across Toronto. It will cost $5.3-billion construction cost, have 25 stops, run 19-km, and has a completion deadline of 2022.
Not wanting to jeopardize its strategic emphasis on customer service and commitment to excellent water delivery and reliability, Toronto Water had to figure out how to manage its assets with this extensive construction project that intersects with existing water infrastructure across the city. To accomplish this, Toronto Water had to develop a streamlined way to collaborate internally but also with outside partners like Metrolinx, as its construction requires Toronto Water to move a large number of assets temporarily or permanently.
When any infrastructure is being moved, the new locations must be recorded and communicated internally and externally to provide service continuity and prevent damages to in-service assets. It is essential that these asset changes are systematically catalogued and tracked, and the traditional mark-up process or documentation in paper logbooks wasn’t nearly sufficient for a project of this scale.
Significant projects and operations require accurate, detailed knowledge of asset locations and relationships. In short, organizations need location intelligence. They need geographic information system (GIS) technology. Moreover, to realize a more complete and accurate view of its infrastructure and improve operational awareness, Toronto Water saw the advantages of collaborating internally, so that all stakeholders, from planning to operations to the field crews on the ground, could both access and contribute to the organization’s GIS.
This was a cultural shift.
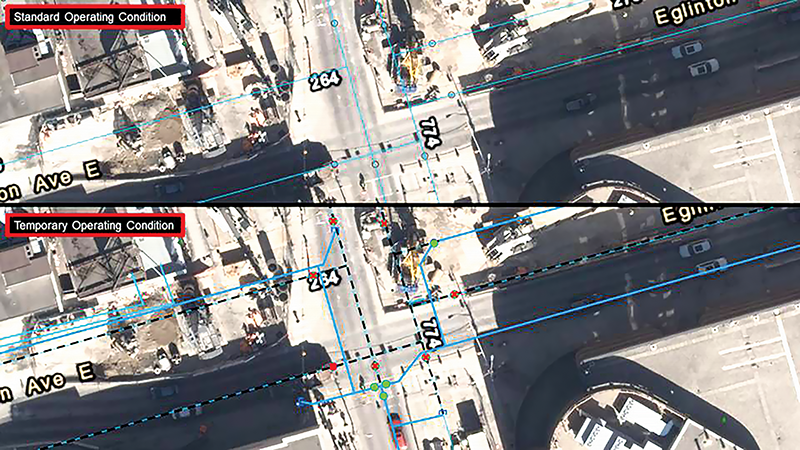
Toronto Water has been using Esri solutions for 10 years. Historically, the Infrastructure Management group was responsible for its GIS. However, the lens through which they view GIS gave a planning perspective rather than a more holistic one that included operations and construction. As such, operations had to depend on infrastructure planning for their location intelligence. Conversely, the planning group did not have access to the most up-to-date construction information, resulting in less than optimal operational awareness as well as lag times required to digitize Records of Alterations (ROAs) and as-built drawings.
To improve operational awareness, efficiency and collaboration, Toronto Water expanded its GIS practice beyond planning to the operations group, which has been instrumental in coordinating with Metrolinx. Operations is now using a connected network and mobile apps so field crews can contribute in near real-time data and as a result, give both planning more up-to-date information and operations more complete awareness of their assets and infrastructure as the Eglinton Crosstown LRT develops.
The distribution and collection group worked with both Metrolinx and Toronto Water field staff to digitize and track changes as to where assets are and how they will be affected by construction, on dedicated map layers, which are then easily shared with all stakeholders.
This means staff can redline assets that will be affected by construction and plan their operations in such a way as to minimize customer impact. Further, they routinely conduct test shuts in advance of construction to validate which customers will be impacted and notify such customers appropriately.
“The Geometric Network has given the operations department the ability to define relationships between assets and how different assets interact with each other as well as perform critical functions like upstream tracing, valve isolation and customer notification,” noted Arash Farajian, policy, planning, and project consultant at Toronto Water.
Field crews are now able to contribute to Toronto Water’s GIS and are directly involved in this feedback process. In contrast to when operations had to rely on Planning for its GIS capabilities, crews now help improve the completeness of Toronto Water’s location data with daily updates to assets. If a main break occurs after hours along the construction route, emergency crews do not need to rely on old, possibly inaccurate data. They can access Toronto Water’s GIS and its Metrolinx layer to accurately assess the situation and resolve the problem efficiently, even if those assets have been temporarily adjusted due to the construction.
Toronto Water has seen that effective management of its location information has improved its ability to collaborate internally and coordinate with outside partners and, in doing so, meet its strategic goal of providing excellent water delivery and reliability to customers, despite an ongoing huge construction site nearby.
This article was written by Brian Bell, the director for utilities at Esri Canada, for the November/December 2020 issue of Water Canada.